最初の依頼は、伝票作成の自動化。しかし、そこだけ自動化しても効果が見えない状況・・・
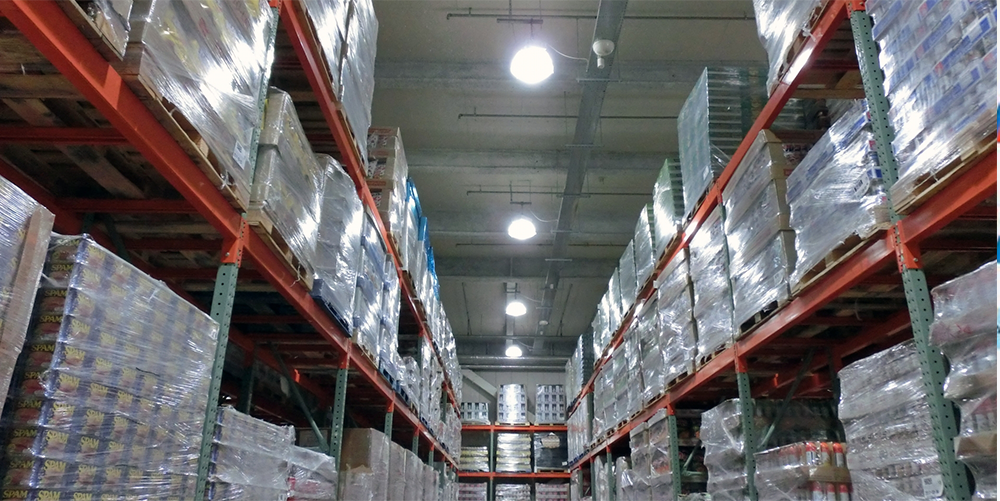
要約:出荷処理を高速化したかったので、出荷伝票を作成するのを自動化できないだろうかと考えましたが、実際には一番時間がかかっているのは倉庫のピッキング作業でした。
当初考えていなかった真の原因を改善することで、劇的に改善した事例です。
ネット販売の出荷処理を高速化したい
ネットショップでの販売が好調で、月曜日や連休明けは出荷処理に膨大な時間がかかっています。
社員の人数的にも、そろそろパンクしてしまいそうです。
受注データから出荷伝票を作るのだけでも自動化することで、処理時間が短縮できるのではないかと考えていました。
どの工程を見直せばいいのか?(業務体系表とパレート分析)
本当に出荷伝票の作成を自動化することで効果があるのか不明だったため、まずは現在の作業でどこに時間がかかっているのか調査を行いました。
出荷処理全体で業務体系表を作成し、さらにパレート分析を使用することで改善効果の高い業務を見つけます。
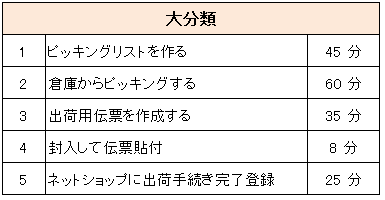
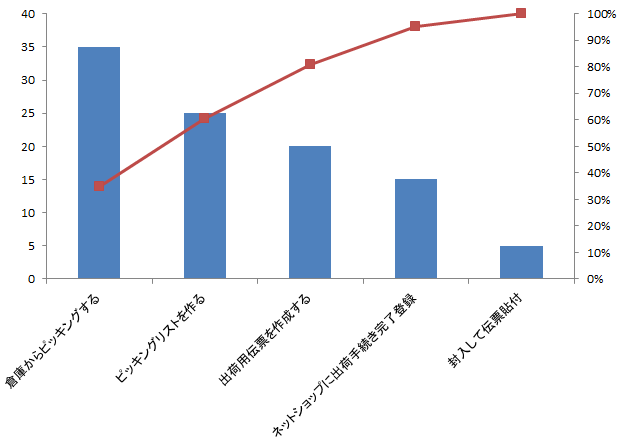
分析の結果、出荷用伝票の作成よりピッキング作業とピッキングリストの作成に時間がかかっていることが見えてきました。
改善すべき業務が見つかったので、次は問題の原因とその解決方法を探っていきます。
数字だけでは見えない問題点(リスク分析)
専任で特化している社員が倒れたら業務が回らない
新人を採用しても、今の業務のままでは慣れるまでに三か月以上かかる
特性要因図で見えた解決の糸口
ピッキング作業に注目し特性要因図を作成し、原因を特定していきます。
ピッキングはなぜ大変なのか?
- 倉庫が狭くてすれ違えない
- どこにあるかわからない
- 他のスタッフが退くまでスライド棚を移動できない
具体的な原因が見えてきました、それぞれの原因を解消することが解決への糸口となりそうです。
改善のポイント!
今まではどこにあるかわからない商品を探し出すために、倉庫内を探し回っていました。
これを解決する方法として1から順に集めて回ればよいように、商品マスタに棚番号を登録
ピッキングリストに棚番号を表示
- 商品マスタの情報に棚番号を追加、保管されている場所を管理します。
- ピッキングリストに棚番号を表示し、どの棚に行けばよいかリストを見るだけで分かるようにします。
- 効率的に回収できる順番でピッキングリストを作成します。
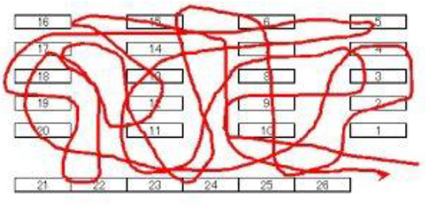
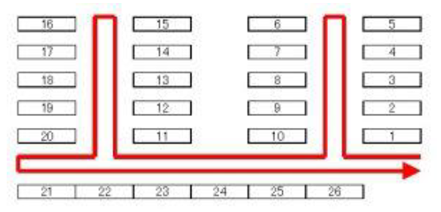
ピッキング担当者が倉庫内でどのように移動しているかをイメージ図にしてみました。
改善を行う前後で明らかな差が出ています。
改善のポイント!
- 標準化とシステムの導入
- 棚番号順に並べたピッキングリストの作成
- どの会社の注文情報でも一元管理されるシステム
- どの配送会社への出荷でも、一元管理ファイルから伝票印字可能
業務改善の効果
今回の業務改善では以下の効果を得ることができました。
- 出荷処理のフローが共通になることで、専任の社員でなくても処理が進められるようになりました
- 新入社員も短期間で処理を覚えることができるようになりました
- 現在は新たなショッピングサイトに出店を進め、業績が向上しています
最初は曖昧だった「出荷処理に時間がかかる」も、きちんと分析して問題を特定することで、最初は考えてみなかった問題が見つかり、改善効果の高い箇所の改善に取り組むことで出荷処理が劇的に変わりました。